iAR Lab Research Direction
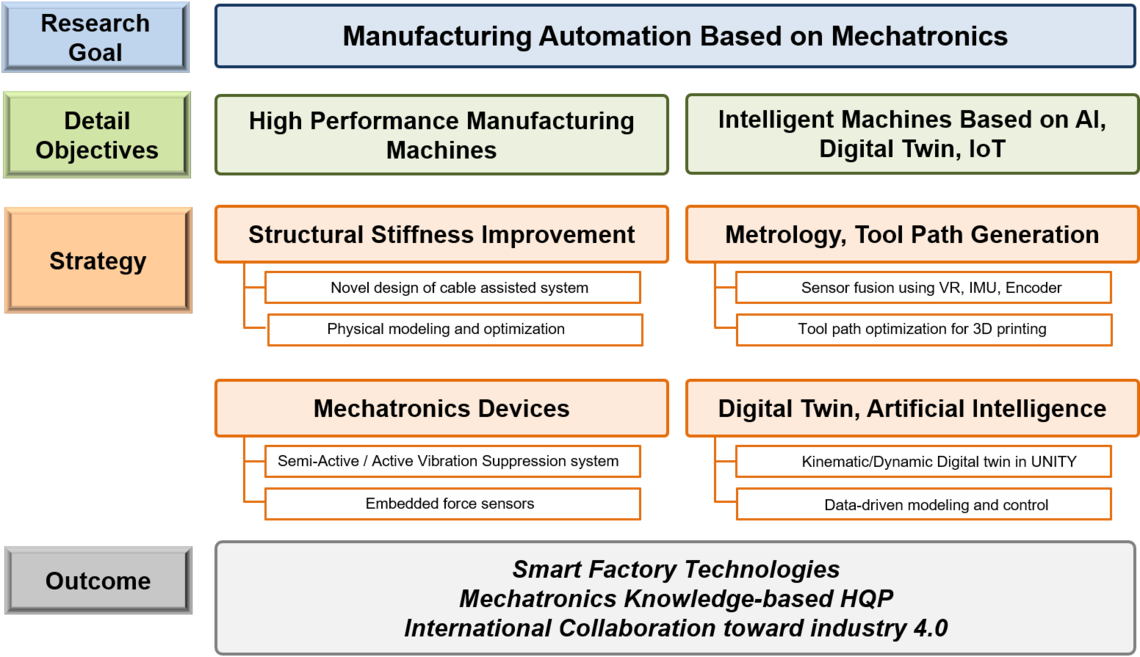
1. Intelligent automation
Cutting force measurement (funded by KIMM)
- Motivation: Need to measure clamping force and cutting force
- Challenge: Embedding sensors, Decoupling Force, dynamic compensation
- Goal: Develop a smart-vise device
- Collaborating with Dr. Park
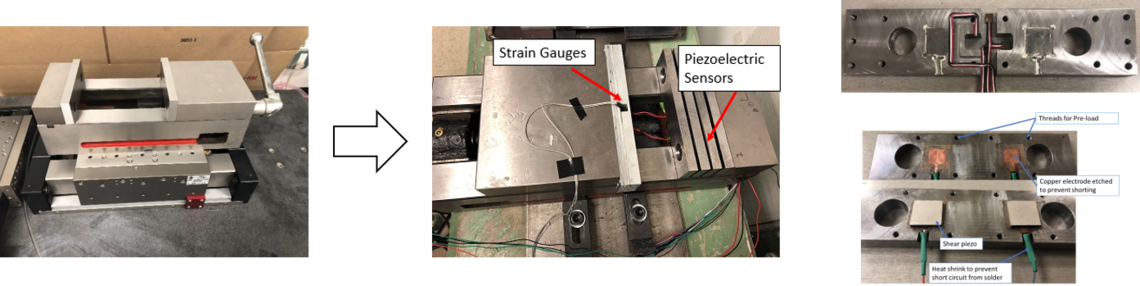
Manufacturing process smart automation (funded by GN Corporation)
- Motivation: Need to automate a certain manufacturing process
- Challenge: A specified system mechanism and vision technology are needed
- Goal: Develop an automated manufacturing process platform
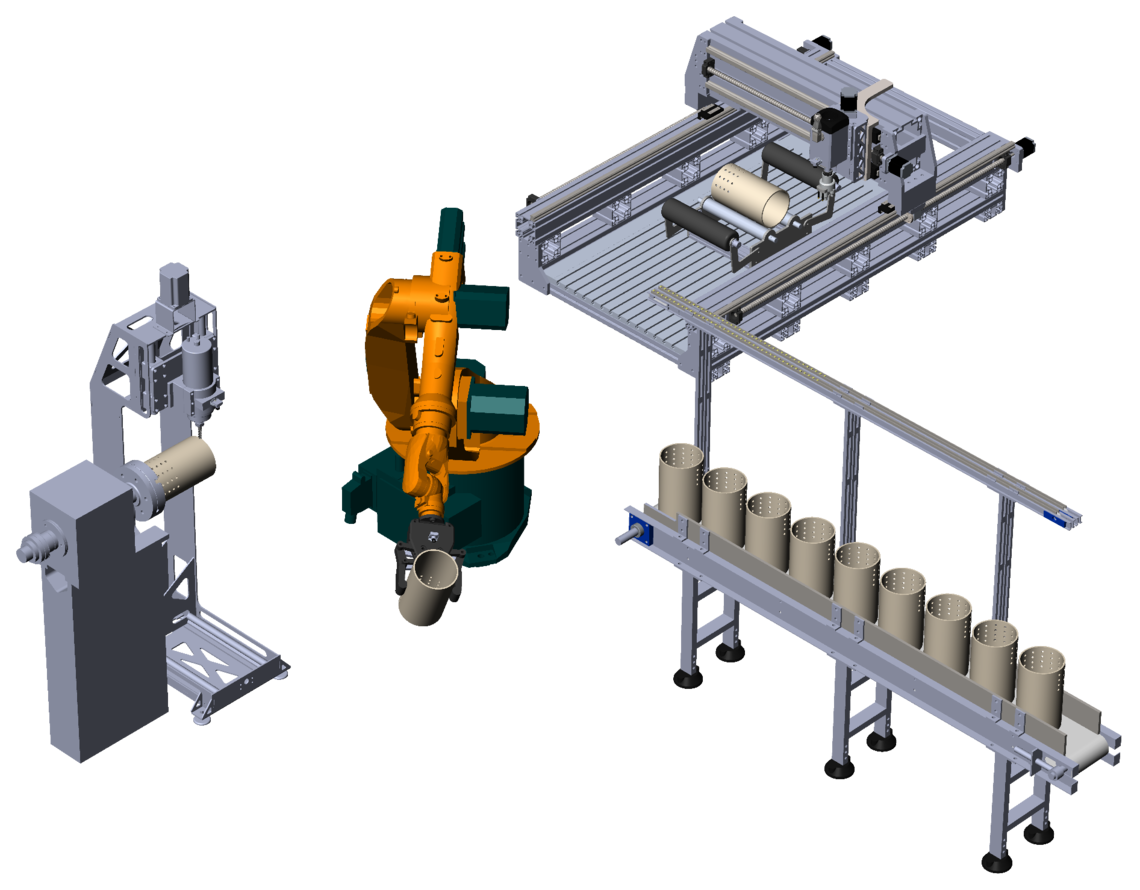
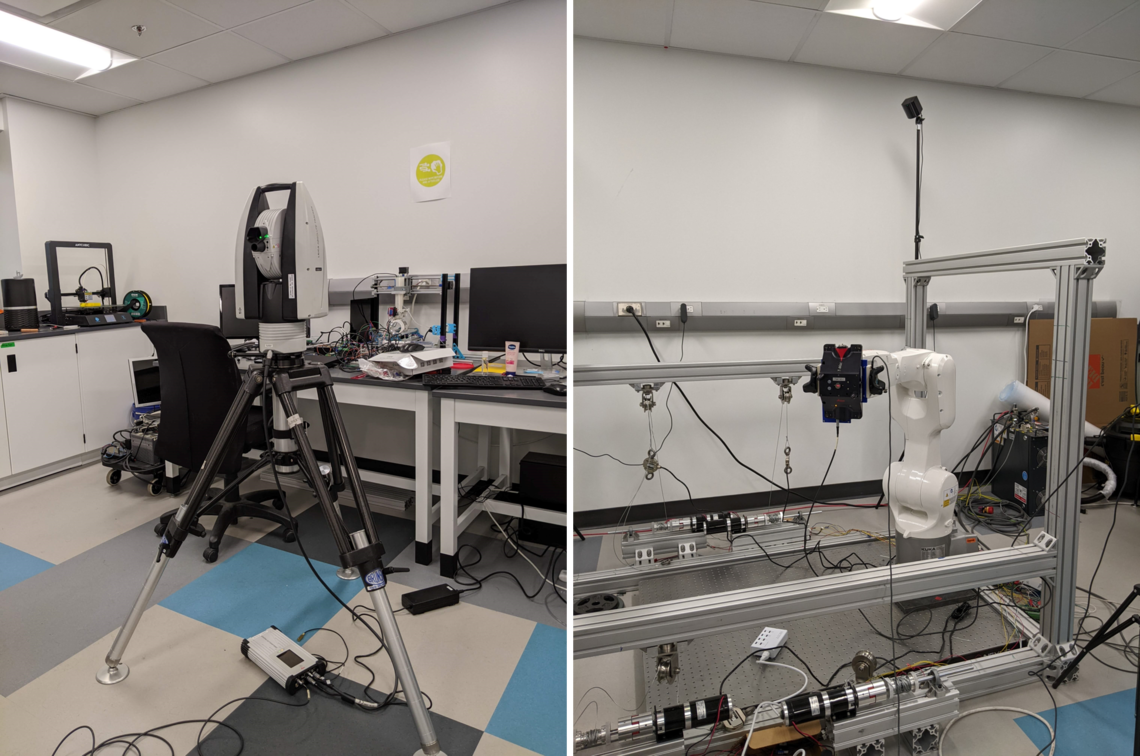
Low-cost and high-accuracy position tracking system (funded by URGC)
- Motivation: Need a high-accurate and low-cost tracking device
- Challenge: signal drift, tilted local coordinates, and low static/dynamic accuracy
- Goal: Develop a tracking system based on VR tracker
Robotic 3D bioprinting with vision system
- Challenge: robotic 3D printing system needs to create and automatically update a tool path
- Novelty: novel bioprinting, vision-based tool path generation
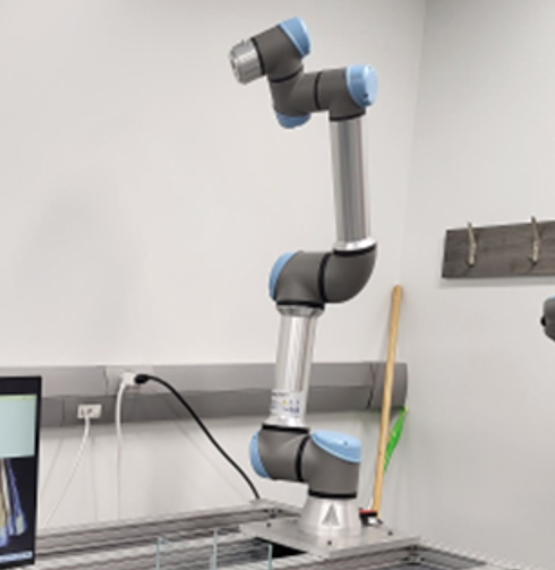
2. Robotic machining
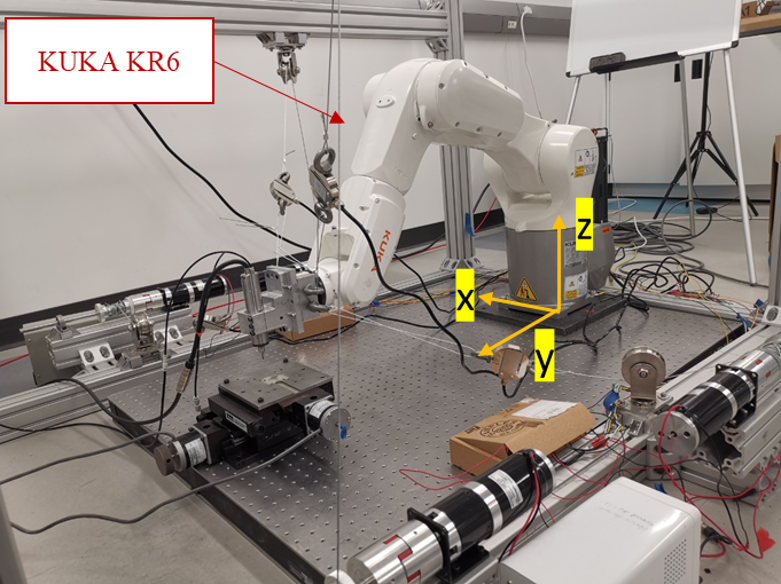
Cable assisted robotic system (Funded by CFI)
- Challenge : 50 times lower structural stiffness than that of CNC machine tools
- Novelty: Installing an optimal configuration of cables at the robot/ Controlling the cable to track the robot’s movement
- Outcome: 5~10 times stiffness improvement , Milling steel using the robot
Static deflection compensation of robotic machining (Funded by KITECH)
- Challenge: Robot is easily deflected while machining
- Novelty: Cutting force estimation using nonlinear disturbance observer & compliance error compensation
- Outcome: 75% reduction of the static deflection
