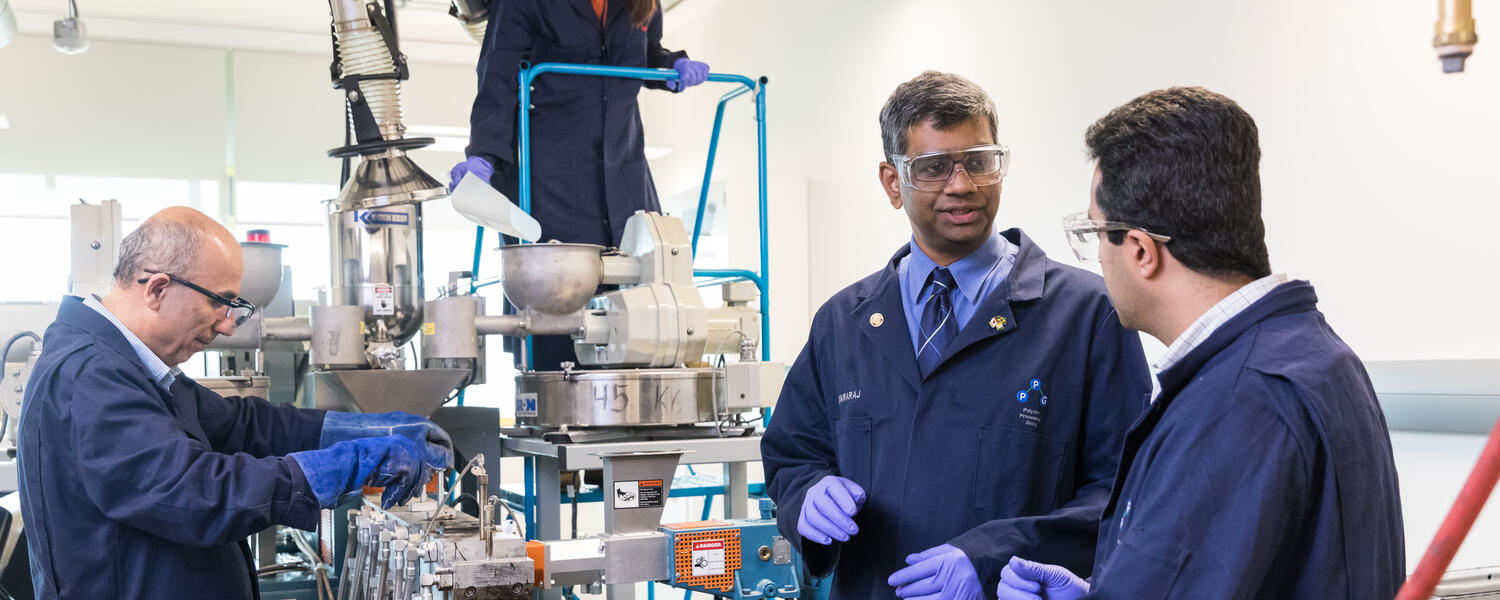
Polymer Nanomaterials
The Centre for Advanced Polymers and NAnotechnology (CAPNA) focuses on new materials:
- Polymer blends: A very efficient way to create new materials with enhanced performance.
- Polymer Nanocomposites: Polymers with nanofillers are being used for high tech applications,
The blending of two or more homopolymers (with or without nanofillers) to form immiscible blends having certain desired mechanical properties is a key scientific challenge that requires application of concepts from chemistry, polymer physics and engineering design. However, very little is understood about the reasons for their outstanding properties and their processing.
How CAPNA has used Nanomaterial Synthesis and Polymer Blending
The group has made polymer nanocomposites using specialty nanofillers produced in-house with tailored size and properties. When combined with polymers, they have unique properties that are suitable for advanced applications. It has been found that these materials offer key combinations of properties not available in single-phase materials. The incredible amount of interfacial area that is available in nanosized materials can lead to novel properties previously unattainable via traditional composites.
Other studies of current interest for the group are related to the understanding of properties and processing of polymer blend nanocomposites made of two or more immiscible polymer blends and nanofillers like carbon nanotubes, carbon nanofibers, graphene, MXene and nanoclays. This is a very exciting, challenging and multidisciplinary area that offers great opportunities for academic and industrial partnerships. See below for more information of different research projects in this area.
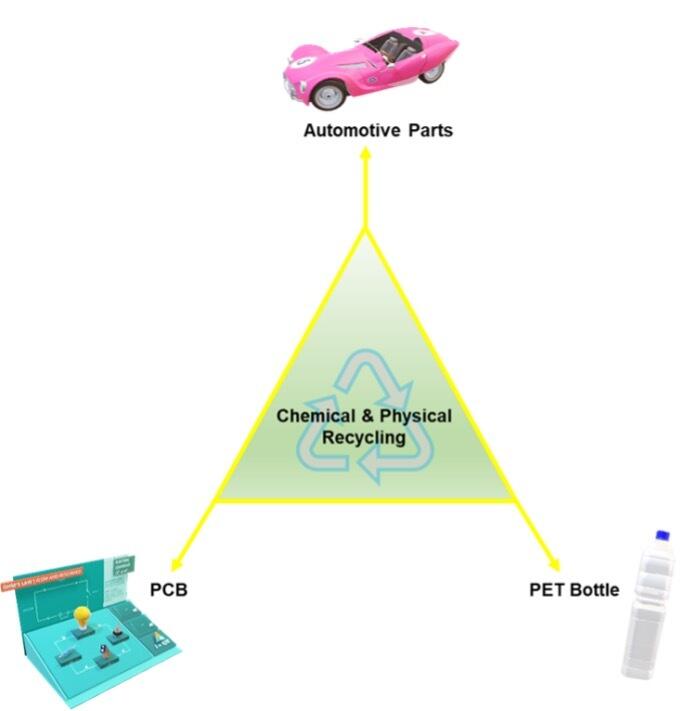
Recycling of Plastics
Recycling of plastics involves the collection and processing of waste plastic materials to transform them into valuable products. Notably, a significant portion of currently used plastics is non-biodegradable. Therefore, recycling plays a vital role worldwide aimed at minimizing plastic waste. Presently, the group is working on both physical and chemical recycling utilizing different waste materials, such as automotive parts, electrical and electronic equipment, packaging materials.
· EPDM bumper waste from end-of-life vehicles (ELVs) is utilized as a filler component to create polymer nanocomposite by melt mixing method with enhanced mechanical, electrical, and EMI shielding performance.
· Non-metallic part of waste printed circuit board (PCB) is employed to obtain oil-based phenolic resin bypyrolysis that exhibits favorable mechanical properties along with a new route for being used as a raw material in electronic devices.
· Recycled polyethylene terephthalate (rPET) is introduced to develop a multifunctional nanocomposite using different nanofillers by melt blending technique.
CAPNA Nanomaterials
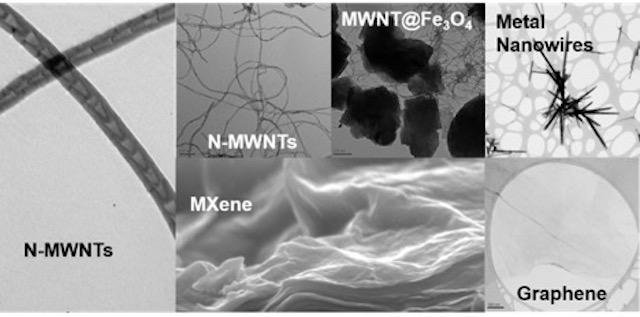
Nanomaterials synthesized in our labs
Polymer Processing
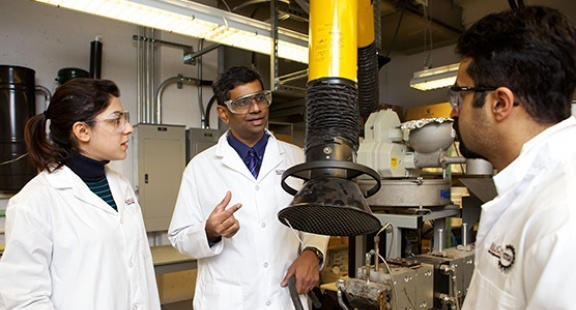
Extrusion
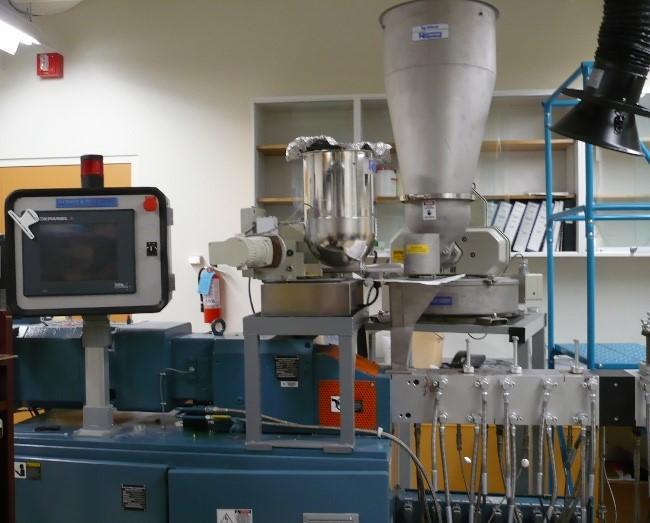
Fundamental chemical engineering concepts like heat transfer, mass transfer, reaction and mixing have not been applied to what is essentially a chemical engineering process - screw extrusion of polymers and polymer blends. Previous work in this area has not attempted a unifying treatment of the twin-screw extrusion process using chemical engineering.
Morphology Development during Extrusion
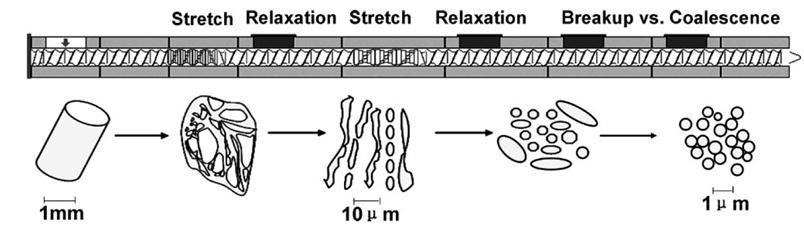
Asphaltene Composites
Known as the heaviest and the most surface-active hydrocarbon fraction of crude oil, asphaltene is the inevitable waste product of the petroleum industry, which causes numerous problems during oil production and transportation. It can be used directly or after its extraction from the heavy oil as an energy source by its combustion. In addition, asphaltene can be used in more advanced materials to produce value-added products and has some characteristics, such as its low cost and rigid molecular structure that make it viable as a reinforcing filler in composites. As a result, we have introduced asphaltene to polymer composites as a low-cost filler to improve their properties.
Nanomaterial Synthesis
We custom synthesize fillers with different functional properties for a wide range of applications such as charge storage, electrical conductivity, EMI shielding, enhanced oil recovery, and sensors.
We can make several types of tailor-made nanomaterials in our laboratory including:
Carbon nanotubes: Undoped and nitrogen-doped CNTs are made using chemical vapor deposition (CVD) method.
Metal nanowires: The template-based electrodeposition method is used to create various metal nanowires with precise control on dimensions in the nanometer scale.
Metal oxide nanoparticles: Hydrothermal synthesis method is used to prepare metal oxide particles.
MXene: We fabricate MXene using a custom MILD (minimally invasive layer delamination) protocol.
Graphene: Graphene is synthesized using a modified electrochemical exfoliation method.
The final properties of nanocomposites are controlled by the functional properties and dispersion quality of fillers in polymer matrix. Desired dispersion of fillers in polymer matrices is achieved using a wide range of processing equipment available at our facility
Miniature Mixer Design
The group has built two new miniature mixer designs to analyze specialty materials available in small quantities (2 grams or less). These custom-designed mixers allow us to synthesize blends and nanocomposites that match those made in larger industrial scale extruders and batch mixers.
Morphology
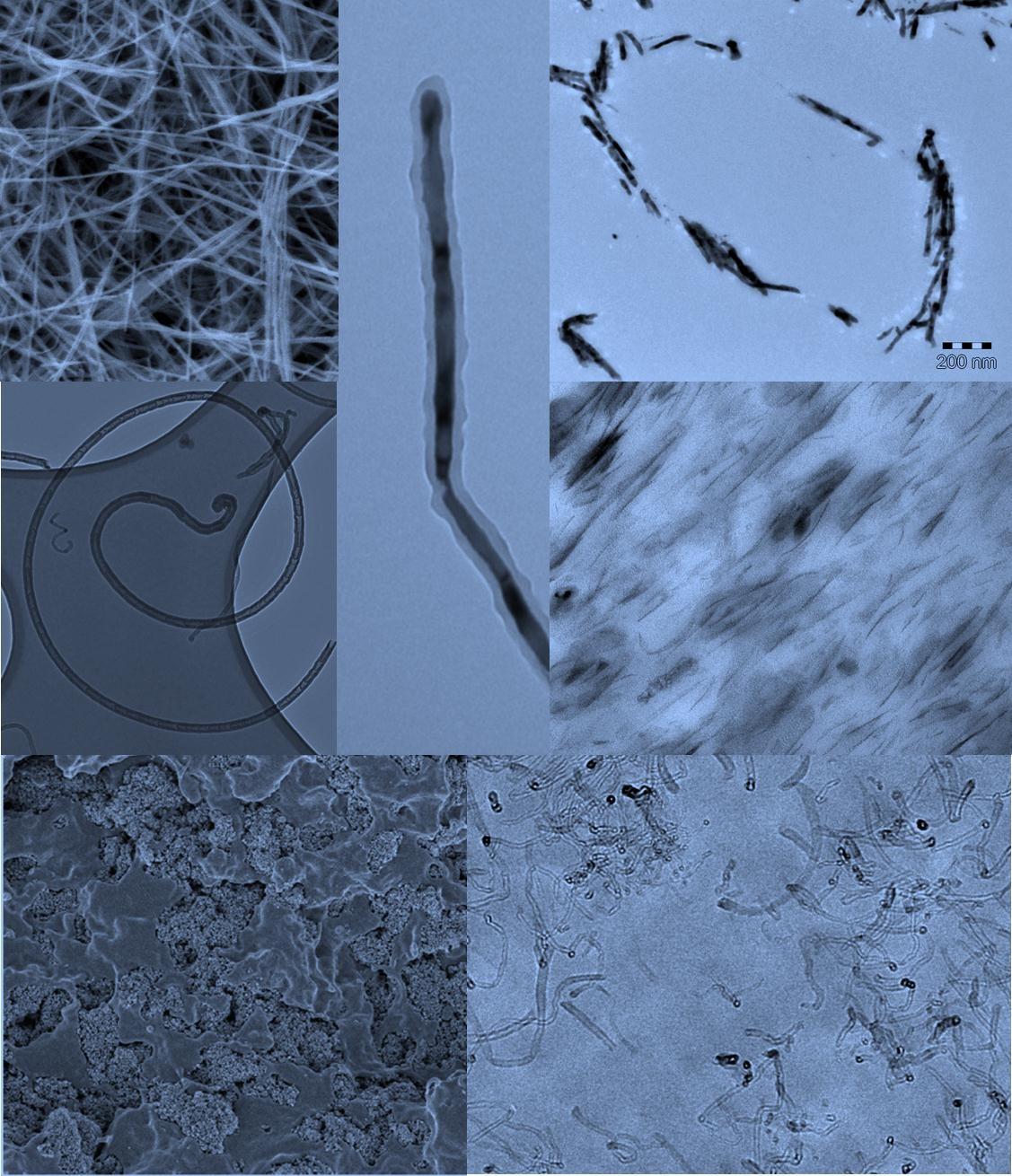
The final properties of polymer blends depend on their morphology, which is in turn controlled by the blending process. It is crucial to understand the mechanisms that control the incorporation of one polymer into another and its relation to the final distribution and properties of the blend. The group has laid out the basic mechanisms involved in the morphology development of a polymer blend: i.e. the breakup and formation of particular structures of a polymer material inside another polymer. The group is performing research on the visualization of melting, deformation, and breaking up of polymers during melt mixing process. Currently, we are modeling deformation of viscoelastic materials and using model experiments to understand the fundamentals. The effects of coalescence and interfacial reaction on the stability of polymer blend morphology have been and continue to be studied.